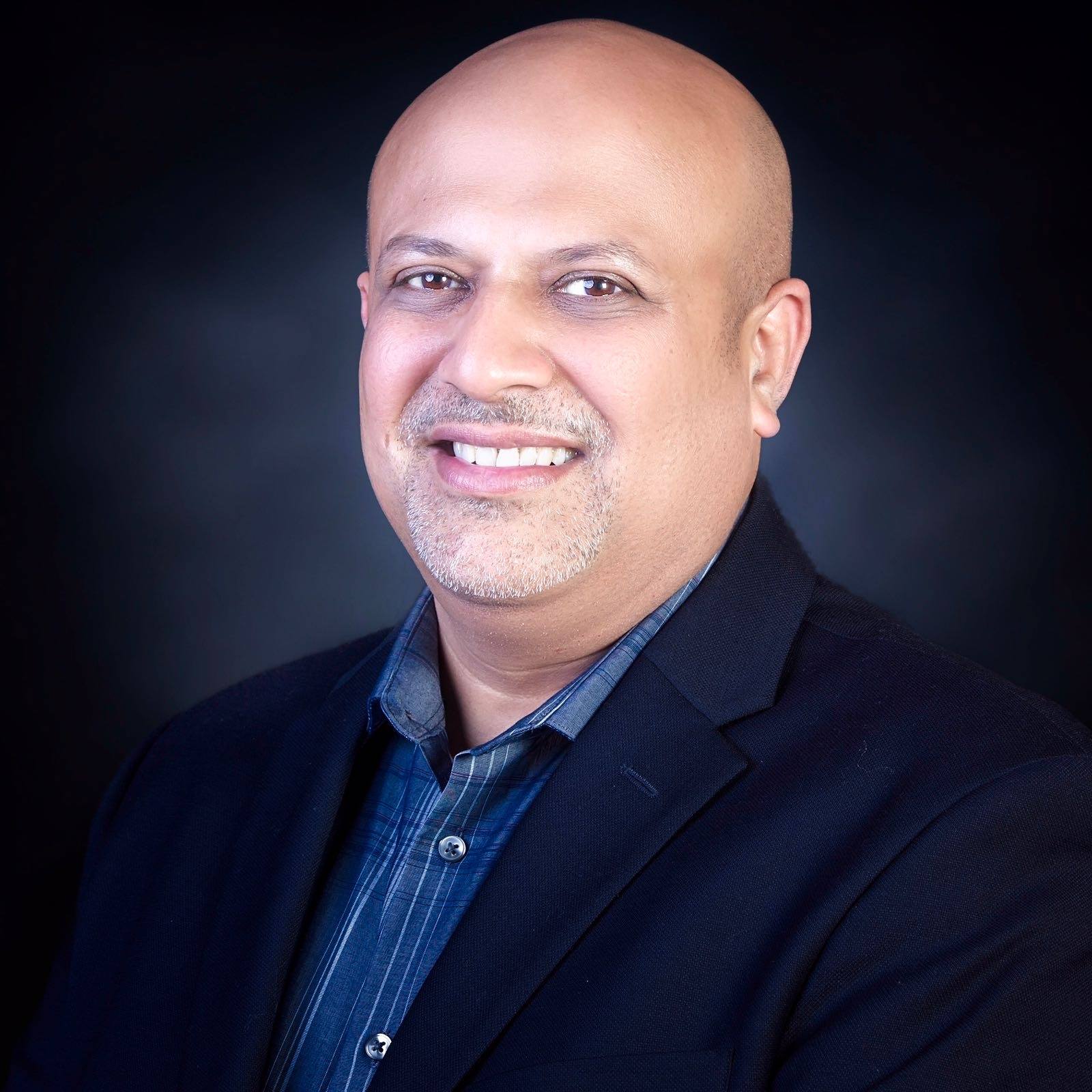
McKinsey & Company describes Industry 4.0 as the next phase in the digitization of the manufacturing sector that is being driven by four disruptions: the astonishing rise in data volumes, computational power and connectivity, especially new low-power wide-area networks; the emergence of analytics and business intelligence capabilities; the new forms of human-machine interaction, such as touch interfaces and augmented reality systems; and the improvements in transferring digital instructions to the physical world, such as advanced robotics and 3D printing.1
Smart and connected things and devices change how products are designed, made, used and maintained, and the impact of Industry 4.0 — as depicted in Figure 1 — can produce strong overall benefits for a business.
Figure 1: The impact of Industry 4.0
Source: Deloitte Insights
The life sciences industry lags in embracing Industry 4.0. This is mainly due to the perceived risks to product quality and patient safety related to implementing any change within its complex validated manufacturing environment(s).
Taking a structured approach to determining an organization’s maturity in digital manufacturing operations can be very helpful in moving forward. It starts with assessing the company’s capabilities based on its agility and capacity to produce and utilize meaningful insights. One approach is 5C, which addresses connectivity, concurrency, coordination, collaboration, and conformity.
Not only can this reference framework help life sciences organizations with in-house manufacturing evaluate their as-is manufacturing environments and assess their digital maturity, but it can help them build a roadmap for successful Industry 4.0 transformation.
Now is the time for Life sciences manufacturing digital transformation
Current trends and the increasingly accelerating rate of change in the industry, as depicted in Figure 2, make it critical for life sciences organizations to insert practical innovation into their business processes and leverage the tremendous volume of data generated within their value chains. These companies must utilize advanced technologies to digitize end-to-end processes or risk competitive disadvantage in a world of collaboration within and across industry verticals.
Figure 2: Four key industry trends2
Source: KPMG International – Future of Life Sciences
Life sciences organizations with in-house manufacturing maintain their manufacturing operations on outdated platforms, with a reluctance to transform to more modern technology due to perceived product quality, safety risks and costs associated with revalidating a working, licensed manufacturing process.
However, a recent Deloitte survey shows that most industry leaders — including those in life sciences — seem to be gaining a much deeper understanding of Industry 4.0.3 They’re increasingly aware of the challenges and now view the actions needed as a success imperative.
Life sciences manufacturing leaders know that safely and efficiently manufacturing drugs or medical devices depends on not only collecting and storing the required data but leveraging it in ways previously not possible. Stakeholders can utilize Industry 4.0 capabilities to sense, predict and automate a variety of functions on the shop floor. Sample use cases include:
– Enhancing overall equipment efficiency and productivity by proactively sensing equipment failure based on run-time data and invoking a predictive maintenance activity
– Sensing a temperature deviation in raw material inventory at the time of receipt from a supplier to reject a shipment
– Using augmented reality solutions for operators to drive root-cause analysis and resolution for assets experiencing an issue on the floor
– Detecting a potential product consistency issue with a tablet mixture based on readings from a humidity sensor
– Analyzing production performance data in real-time and recommending actions to:
– Improve production processes by reducing planned downtime and breakdowns
– Lower loss of production velocity and changeover time
– Drop overall production and startup rejects
Although the understanding of Industry 4.0 concepts has been spreading swiftly, the scope of the problems it can solve, and the technology required to do so, can quickly become overwhelming. Organizations need a structured approach to understanding digital maturity and assessing capabilities.
Figure 3: 5C Approach to Industry 4.0
The 5C approach to Industry 4.0
The ability of any manufacturing operation to dynamically adjust its performance depends on five tenets (or the 5 Cs):
1. The connectivity to capture information in real or near-real-time from the interactions that occur between people, partners, processes, and assets while a product moves through the manufacturing cycle.
2. The data gathering and analytical capabilities that account for the concurrency of all the processes in play at a given point in time.
3. The ability to sense and measure exceptions for proactive coordination of corrective actions within in-house or with contract manufacturing organizations
4. The cognitive capacity to understand the need for the collaboration required between internal and/or external stakeholders and instantiate it, especially in a contract manufacturing scenario
5. The ability to conform to the required quality, security and performance standards.
Connectivity determines how ready the as-is manufacturing environment is to allow the real-time capturing of relevant performance information at every measurable step of interaction between the process, the assets, and the product.
The focus of this tenet is to develop an understanding of the already available data and the relevant data points that aren’t currently being captured to assess the state of manufacturing in real-time— and the application of technology levers required to establish interconnectivity. Simultaneously, companies need to define the actionable insights that can be acted upon in real-time to enhance the efficiency of a given environment.
For example, determining the particle size in the production of a capsule may require the company to consider the humidity of the factory where its milling machine operates. If the humidity reading for that area isn’t readily available, special humidity sensors may be installed to capture and feed that data at any point in time. The connectivity from these sensors should enable data gathering and action in real or near-real time to make a true difference.
Concurrency is imperative to understand the ongoing, simultaneous activities or tasks in the context of the as-is manufacturing environment and the impact of their success and failure on each other. Enabling data science to gather real-time information and insights on these related activities and tasks can help drive a much-needed action or activity to render positive outcomes for either of the processes or subprocesses. This tenet takes the timing of data gathering and the generation of actionable insights into consideration to ensure smoother simultaneous execution of processes in the given environment.
The drug crystallization process control in pharmaceutical manufacturing is a good example of this. Managing crystallization processes requires control of the crystallization kinetics (both nucleation and growth) and the ability to manipulate the kinetics to achieve the desired process result. It’s important to capture and analyze control data points for nucleation and growth concurrently and to generate insights or actions to stop any detrimental effects of either subprocess going wrong on the other.
Coordination is the data science-driven orchestration of ongoing activities within the as-is manufacturing environment. It’s based on real-time dynamics of the production steps and the working environment needed to produce a quality product. The sequence of the activities, including the different participants and their timing (be it an interchange between assets or movement of the work-in-progress product or key production data interchange with contract manufacturing organizations), must be clear to capture information on the go. Eventually, the insights produced with the captured information are utilized to automate and harmonize the manufacturing processes.
In pharmaceutical manufacturing, the timely orchestration of capacity adjustment at the milling process stage based on real-time yield information for a given production batch is a good example of the coordination tenet.
Collaboration governs the actionable insights generated by applying the 5C approach. These insights require timely execution — requiring teamwork — to have a positive impact on overall equipment effectiveness or product quality. For example, if the predictive maintenance and anomaly detection algorithm determines that an asset is going to break down in the near future, then the shop-floor manager in charge of the production process receives an appropriate alert stating that a predictive maintenance action has been generated for the asset in question and that its execution needs to be coordinated as soon as possible with the asset operator and the asset maintenance teams. The collaboration tenet focuses on identifying and mapping possible use cases where coordinated teamwork successfully resolves anomalies. This information can also be fed as a critical input to machine learning algorithms for resolving future-state problems on the shop floor, promoting continuous innovation.
Conformity applies to the manufacturing processes governed by GMP guidelines for engineering standards and 21 CFR 11 for control, data handling and validation compliance. It’s critical to consider all regulatory requirements when digitizing each manufacturing subprocess and to determine the measures that need to be put in place to satisfy a given operation’s cybersecurity needs. This tenet focuses on capturing information about the in-place as-is controls within the manufacturing environment and analyzing this information to identify opportunities for digitizing and expanding control. This, in turn, helps to plug the gaps discovered and, in the process, makes the organization more risk and compliance savvy.
Using the 5C method to evaluate an as-is manufacturing operation should help life sciences organizations understand the digital maturity of their operations. It enables companies to identify the requirements needed to establish a basis for Industry 4.0 processes and further it to achieve universal manufacturing excellence. In addition, the 5C method helps companies focus investment dollars to reduce the overall cost of quality and enable them to increase contextual control over the end-to-end production process and remove risk.
About Chetan Kothari
Chetan Kothari is Director of Business Consulting with the Life Science Division of NTT DATA Services. He has more than 25 years of overall consulting experience including 10 years in the Life Science industry and has led complex digital engagements that enabled visibility and collaboration for large Pharma and Med Device organizations in their supply chain and manufacturing operations.
References:
- Cornelius Baur and Dominik Wee, McKinsey’s Munich office: Manufacturing’s Next Act https://www.mckinsey.com/business-functions/operations/our-insights/manufacturings-next-act
- Ajay Sanganeria: KPMG, Head of Life Sciences, International Tax Partner – The Future of Life Sciences Teams in the Asia Pacific – https://home.kpmg/sg/en/home/insights/2019/03/the-future-of-life-sciences-teams-in-the-asia-pacific.html
- Punit Renjen. “How leaders are navigating the Fourth Industrial Revolution.” Deloitte Insights. January 20, 2019. https://www2.deloitte.com/us/en/insights/deloitte-review/issue-22/industry-4-0-technology-manufacturing-revolution.html